Real-World Validation: Integrity in Clinical Product Evaluations
Tuesday November 19, 2024
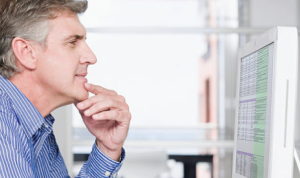
By: Anne Marie Orlando, RN, RCIS, CVAHP
A key function of an effective value analysis or supply chain process is conducting clinical product trials, whether for new product implementation or manufacturer product conversions. These principles also extend to staff education and competency development. One critical aspect of successful trials is ensuring that products are tested in the actual environment where they will be used. This step is essential for several important reasons, which are outlined below.
Evaluating products in their intended environment ensures an accurate assessment of their usability and performance. In a clinical setting, staff need to work efficiently and quickly, often under pressure. Testing products like disinfecting agents, exam gloves, defibrillator pads, and other supplies within the hospital setting allows us to evaluate whether these products perform reliably under the specific conditions they’ll face in day-to-day hospital use. A product that performs well in a controlled environment, such as trialing a cleaning agent or gloves at a conference or your home, may fail to meet the demands of a high-stress, high-frequency hospital environment.
Healthcare facilities must comply with strict standards regarding safety and compliance. By testing products in the actual environment they will be used, we can identify any potential compliance issues before full implementation. This ensures they meet safety standards, reducing the risk of regulatory non-compliance.
Certain products like disinfecting agents, require the hospital’s unique environmental factors—such as ventilation and hospital-grade surfaces. These disinfecting agents must be EPA registered and require validation for use by many equipment manufacturers. Any variation in product testing can affect their performance. Testing in the intended environment provides insights into how these products respond to such variables, ensuring they’re effective and compatible with hospital operations.
Engaging healthcare professionals in the actual environment allows them to provide real-time feedback on ease of use, efficacy, and practicality. Staff may find that certain products do not meet the needs of their specific workflows, or they may identify ergonomic or functional issues that aren’t apparent outside the hospital. This input is invaluable for determining which products are most effective and practical for actual use. Ensure this feedback is collected in a way it can be analyzed and reviewed with specifics, not anecdotally stated.
Products tested and selected without hospital-specific trials may lead to increased waste if they’re ultimately found unsuitable. Reallocating resources to purchase and test products in the hospital reduces the risk of adopting items that incur unexpected costs due to waste, inefficiency, or lack of compatibility.
Since the end goal is to improve patient outcomes, testing products in the environment where they will be used ensures they contribute effectively to patient care. For instance, the application of a certain dressing or the effectiveness of a disinfecting agent can impact infection control measures, which are critical in hospitals.
Overall, hospital-based testing aligns product selection with real-world usage, helps control costs, improves staff efficiency, and enhances patient outcomes—factors that are crucial for any healthcare value analysis team or supply chain operation focused on delivering quality patient care.
Want to learn more about Blue.Point? Contact us today for a free product demo or for more information contact Jennifer Doty by email jdoty@bluepointscs.com or call 978-747-1529.